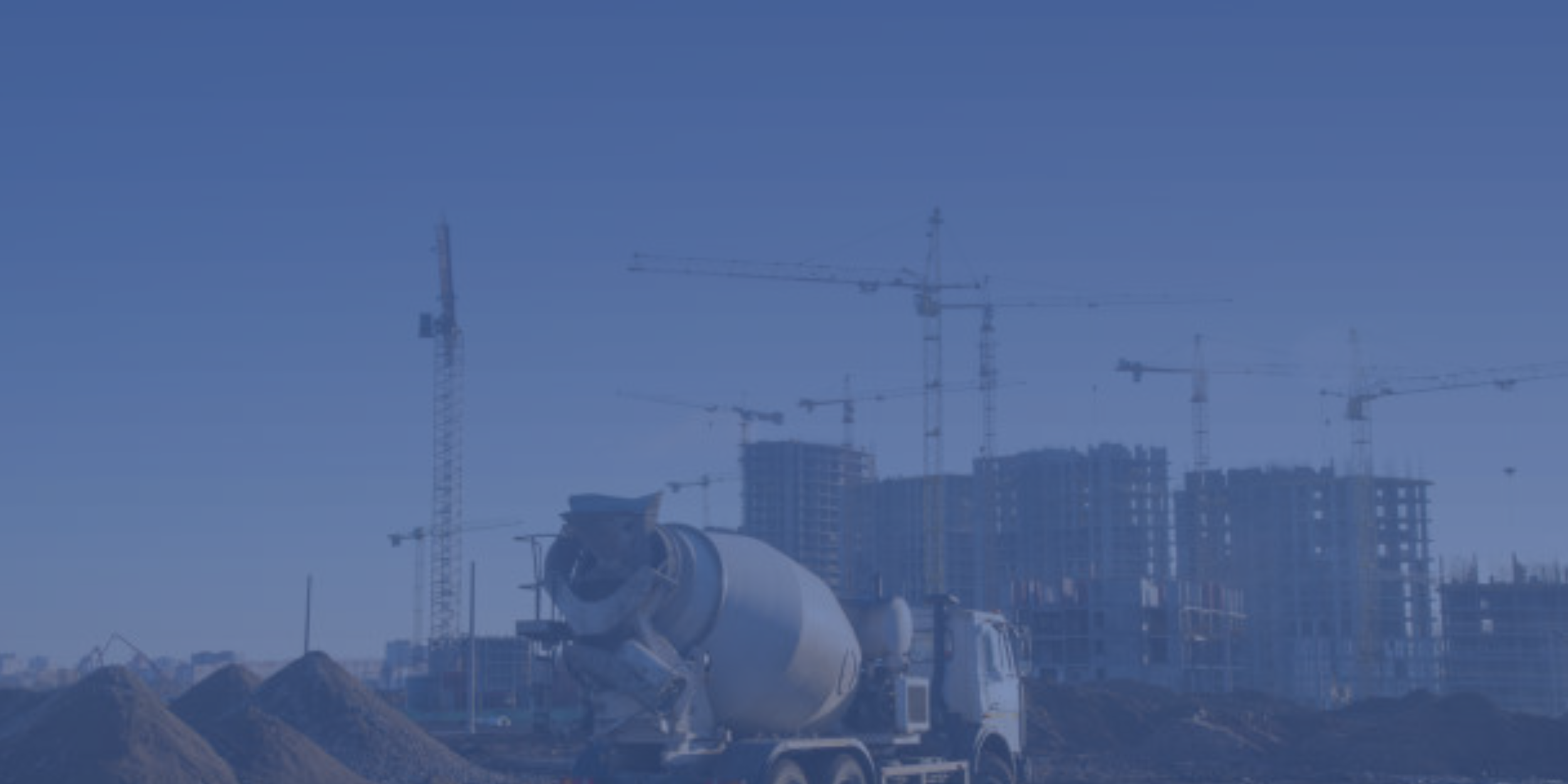
Concrete
Chillers offer several benefits in the concrete industry by providing precise temperature control, ensuring consistent quality, improving energy efficiency, extending equipment life, and enhancing the overall workability of the concrete.
Key benefits of using chillers in the concrete industry:
Temperature Control: Ensure optimal curing temperature for concrete.
Extended Equipment Life: Prevent wear on mixing equipment, reducing maintenance.
Reduced Cracking: Mitigate thermal cracking by controlling temperature.
Consistent Quality: Maintain uniformity in concrete properties.
Improved Workability: Controlled temperature enhances concrete workability and finishing.
Installation Options:
Plate to Plate Heat Exchanger
Heat Recovery
EC Fans
Tanks
Pumps
Electronic TX Valve
Stainless Steel Panel
Standard Factory Options:
Single or multiple pumps
Evaporator shell anti-corrosion internal coating
304 or 316 stainless construction
Pressure and temperature gauges
Copper fin condenser coils
Soft start control (CA10-CA80)
Heat recovery system
Fluid/fluid heat exchanger for process cooling
EC condenser fans
Chiller with remote condenser
Alternative refrigerants (R407F, R134a)
Marine condenser (CW unit)
Condensing unit (CU unit)
Water-cooled condenser (CW unit)
Electronic Expansion Valves
Buffer tank 200L, 400L, 1000L & 2000L
Protection Louvres