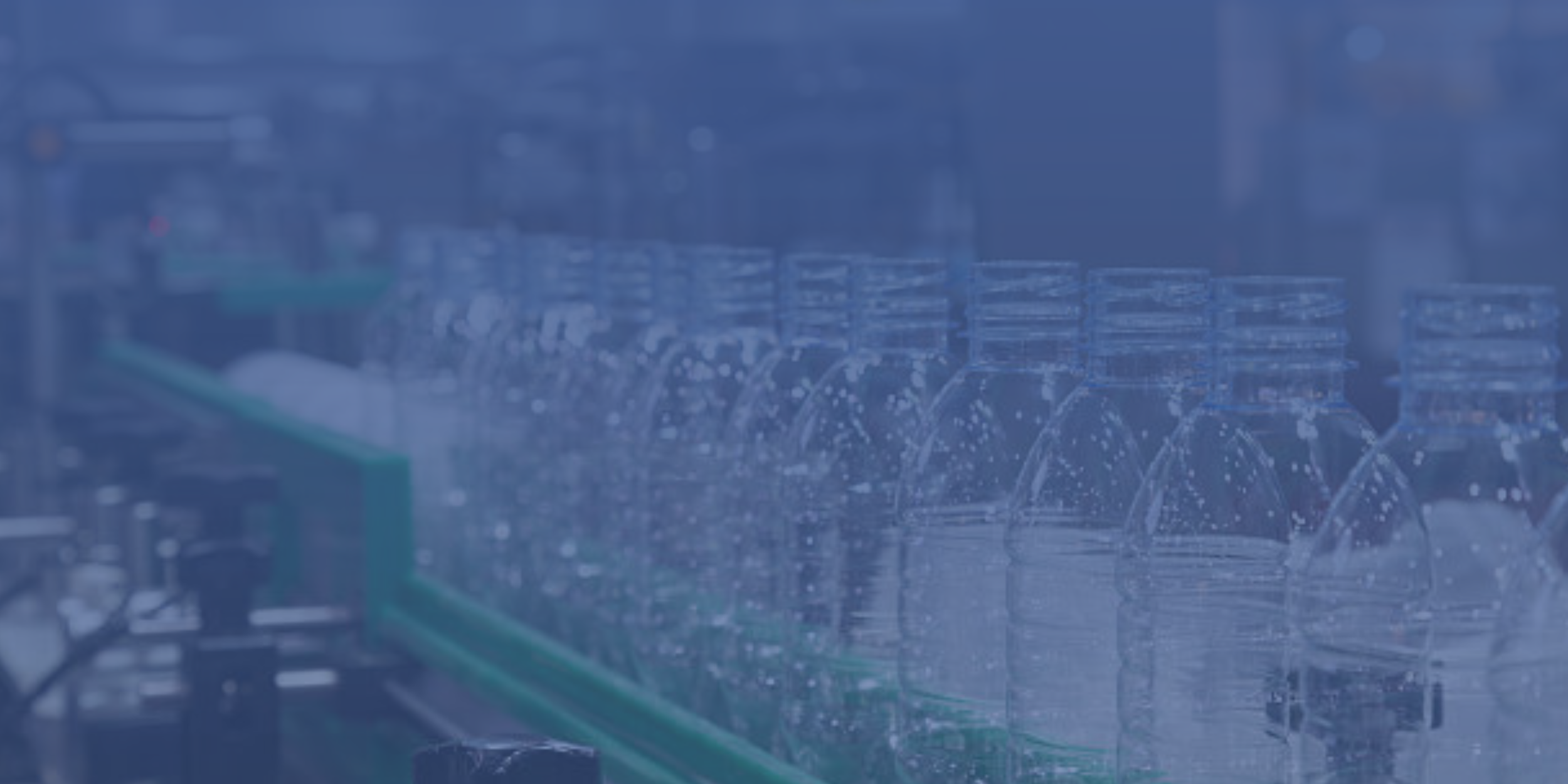
Plastics
Chillers play a crucial role in the plastics industry by providing temperature control that includes moulds and materials.
Here are some key benefits of using chillers in the Plastic Industry:
Mould Cooling: Chillers cool moulds during plastic moulding, preventing issues and ensuring good quality.
Material Cooling: Chillers cool plastics after shaping, improving their properties and final product quality.
Energy Efficiency: Chillers save energy by efficiently maintaining the right temperatures in Plastic Manufacturing.
Temperature Control for Resins: Chillers ensure proper temperatures for different plastics, maintaining product quality.
Reduced Downtime: Chillers' steady temperature control reduces downtime, boosting productivity.
Environmental Control: Chillers help achieve the right temperatures for processes, enhancing product quality.
Process Flexibility: Chillers adapt to different needs, crucial for handling various plastic types.
Quality Assurance: Chillers' precise temperature control ensures consistent high quality, vital in industries like automotive or medical devices.
Installation Options:
Plate to Plate Heat Exchanger
Heat Recovery
EC Fans
Tanks
Pumps
Electronic TX Valve
Stainless Steel Panel
Standard Factory Options:
Single or multiple pumps
Evaporator shell anti-corrosion internal coating
304 or 316 stainless construction
Pressure and temperature gauges
Copper fin condenser coils
Soft start control (CA10-CA80)
Heat recovery system
Fluid/fluid heat exchanger for process cooling
EC condenser fans
Chiller with remote condenser
Alternative refrigerants (R407F, R134a)
Marine condenser (CW unit)
Condensing unit (CU unit)
Water-cooled condenser (CW unit)
Electronic Expansion Valves
Buffer tank 200L, 400L, 1000L & 2000L
Protection Louvres